Owen Stephenson.
An Aspiring Engineering Intern.
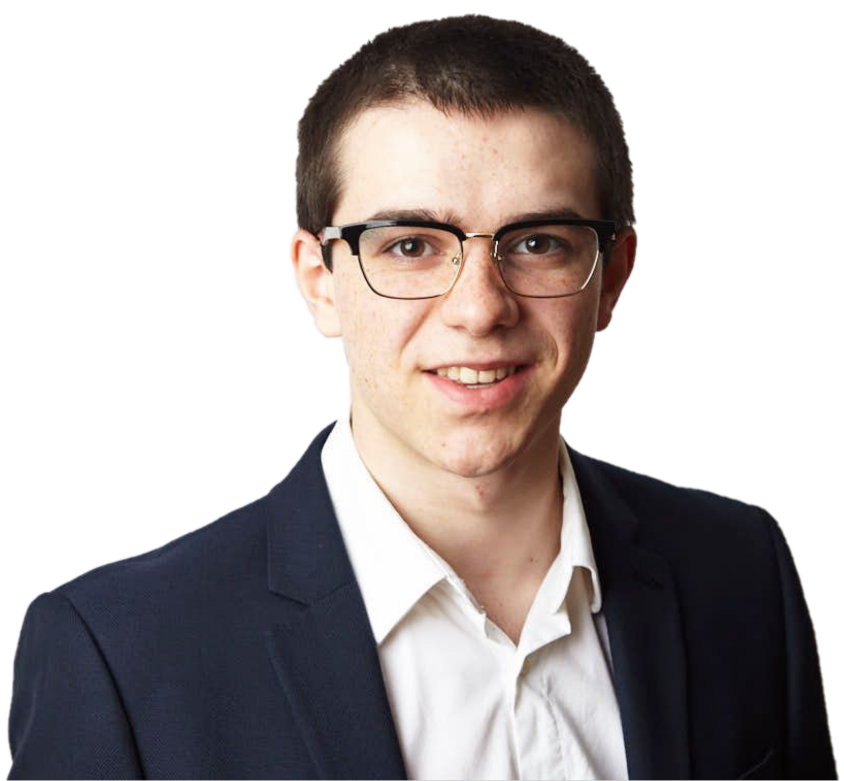
How's it Going
I’m currently studying to earn a bachelors of applied science specialising in Mechatronics engineering at the University of Waterloo. As a part of this degree, I've recently completed my 5th co-op term with Airbus Atlantic as a Design and Manufacturing Engineer. This position allowed me to put to use my various skills in mechanical, and software engineering to optimize processes within their worldwide manufacturing network and do some mechanical design for various aerostructure parts. One of the biggest challenges I faced at Airbus was working in an office full of french speakers, my french improved exponentially and I had lots of fun in the new language environment. Before this, I completed my 4th co-op placement as an Engineering Analyst with Toyota Motor Manufacturing Canada which introduced me to the mass manufacturing world and with it the principles of lean manufacturing. Also, I completed a co-op placement as a Hardware Engineer for Foresight Insurance Analytics, a small startup based in Toronto, Ontario. I'm hoping to further my career as an engineer in the aerospace, aviation, and automotive industries and am currently developing my own model of a turbofan engine with my personally designed gearbox.
My Skills
Computer Automated Design
Programming
FEA & CFD
Projects Done
Internships
Programming Languages
Cities
My Projects
- Device mounting bracket
- This bracket was designed by myself in SOLIDWORKS for Foresight Insurance Analytics. It is being used to mount devices
to a drawer at a specific angle. This bracket interacts with some pre-fabricated components. There are two components, one is the face of a
drawer slide and the other is a heat insert which a handle will mount to. This part was designed with specific attention to its manufacturability
using a 3D printer. This was accomplished by always using fillets instead of sharpe edges which are easier to print. Also, lots of material was
removed from the bracket to reduce the printing time. In addition, the part was designed so it would have a geometry that could be 3D printed
as if it were being extruded so as to reduce to amount of support material needed. Last, this part was printed using PLA which provides high
strength and rigidity while still remiaing lightweight, all of which are important for its application of holding a device securely.
Download
- Model Wind Tunnel
- This summer (2023), I have been working on building a model wind tunnel to characterize some airfoils I 3D printed. The wind tunnel's body is made out of smooth particle board and plexiglass. There is also an array of PVC piping; this is to ensure the air flow is as laminar as possible. I have designed and printed a force measuring device that uses a force measuring resistor to evaluate the lift performance of each airfoil. The circuitry for this lift measuring device was made with an Arduino. The logic for the circuit was coded by myself in C++. The exterior surfaces of the lift measuring device interfere with the wind tunnel, so it was designed specifically to have a low Reynolds number. A low Reynolds number will ensure it introduces the least amount of turbulence possible to maintain the integrity of my tests. This project taught me a lot about aerodynamics and the specifics of how lift is generated. I wrote a detailed report summarizing the research I conducted on this subject before commencing this project. It will be available here shortly.
- Self Stabilizing Model Rocket
- I started this project during my first co-op term and am currently working on it. My vision is to design a model rocket that uses thrust vector control to maintain steady flight. I have played with model rockets before which simply use three fins at the base to maintain steady flight. To design a rocket using this stabilising system seemed too trivial a project to undertake. As of August 2022 I am currently working on integrating all the electrical components together, these include a 3 axis gyroscope and accelerometer, an altimeter, 2 servo motors, and a micro SD card module. These are all combined using an arduino Uno board and will be the brains of the rocket. I have already programmed a basic algorithm to manipulate the angle of the rocket. Development on the body of the rocket, the engine, parachute deployment system and refinement of the code still needs to be done.
- Carbon Capture and Storage System
- This project was submitted to the Innomasters engineering mentorship program through the University of Toronto chapter of Engineers Without Borders. In the year 2020 it was the winning project. This project aims at improving the current methods of carbon capture and storage. No system that currently exists has any satisfactory method of safely storing the carbon dioxide (CO2) once it is removed from a flue gas. My group's design uses a carbon mineralization technique using a chemical called serpentine to form a mostly inert mineral that is harmless to the environment. In addition, our design uses charged electrochemical plates which have a polyanthraquinone coating which contains carbon nanotubes that have a natural affinity for CO2. The system is far better than the widely used industrial wet and dry scrubbers due to the fact that it can remove CO2 from a flue gas from very low concentrations including atmospheric air. This design is a combination of various research projects not done by myself, my group and I put them together with various modifications to form one coherent design that can capture and store CO2 safely. We designed the entire system using Fusion 360.
Contact Me
Toronto Waterloo, Canada
Phone: 647-208-4917
Email: stephenson1owen@gmail.com
Have a question? Let's get in touch, Send me an email or text anytime!